Process Improvement: Optimizing your Business Processes
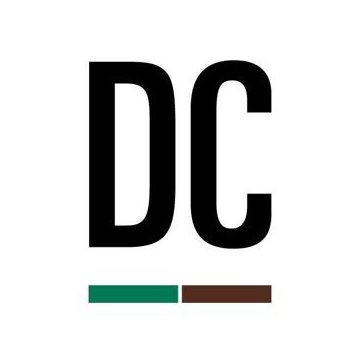
Timeline
-
February 12, 2024Experience start
-
March 30, 2024Experience end
Experience scope
Categories
Data analysis Supply chain optimization Operations Product or service launch Product managementSkills
project planning supply chain management business consulting business process improvement researchStudent teams from Durham College’s - Process Improvement II course will work with your organization to analyze a challenge currently affecting your organization, and develop a solution that improves quality and/or processes for your organization.
Learners
The final deliverables will be agreed upon in at the project scope meeting and will vary by project. Generally, your organization will receive a report, live presentation, or project plan.
Project timeline
-
February 12, 2024Experience start
-
March 30, 2024Experience end
Project Examples
Requirements
Students will work in teams of 3 and spend 10-15 hours per student working with your organization to support the development of improved quality and/or processes that your organization can execute to get results.
You will need to provide the students with a goal, issue, or gap to focus on. Areas of focus include, but are not limited to, manufacturing, quality assurance, supply chain management, and customer service.
What our students could help with:
- Collect data in relation to an existing problem i.e. customer complain, late delivery, defective parts, etc. By using techniques like brainstorming, focus group, survey, etc.
- Apply SPC in a particular control chart to both service and manufacturing for both available and attribute data in order to analyze data behavior and process variation.
- Apply Process Capability study manufacturing processes in order to verify that the process is capable and risks are evaluated.
- Apply a statistically valid acceptance sampling and calculate the producer’s and consumer’s risk due to the sampling procedure.
- Create a policy and procedure for the measuring system in manufacturing and conduct Repeatability and Reproducibility gage study to validate the measuring system.
- Apply 7 quality tools i.e. fish and bone, Pareto chart, house of quality, flow chart to collect, organize and analyze data.
- Apply some management tools
- Assess/analyze risks by constructing a FMEA (Failure Mode and Effect Analysis) to any service or manufacturing product/process.
- Assess the effectiveness of the current layout and design/suggest a new layout for any manufacturing or office/clinic facility.
- Review and modify or create a new purchasing policy/procedure base on the company’s needs and requirements.
Some project examples include:
- How do we reduce waste and variation and improve productivity in storerooms, office supply rooms, or production lines? (i.e. through a 5S program)
- Turn-around-time has increased and does not meet customer requirements. How can we improve turn-around time by 10%?
- The intake process for Clients/Customers has a high incomplete/error rate. How do we reduce the number of errors on the intake form?
- How can we better understand value from the customer's perspective? Students can perform Voice of the Customer/Critical to Quality analysis to determine what matters most to your customers.
Additional company criteria
Companies must answer the following questions to submit a match request to this experience:
Additional company criteria
Companies must answer the following questions to submit a match request to this experience:
Timeline
-
February 12, 2024Experience start
-
March 30, 2024Experience end