Process Improvement: Optimizing your Business Processes
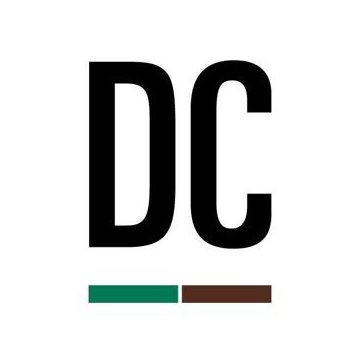
Timeline
-
February 16, 2021Experience start
-
February 16, 2021Project Scope Meeting
-
March 2, 2021Progress Check-in Meeting
-
March 23, 2021Experience end
Timeline
-
February 16, 2021Experience start
-
February 16, 2021Project Scope Meeting
Meeting between students and company to confirm: project scope, communication styles, and important dates.
-
March 2, 2021Progress Check-in Meeting
Meeting with the students and instructor to review project progress.
-
March 23, 2021Experience end
Categories
Operations Project management Product or service launchSkills
project planning supply chain management business consulting business process improvement researchStudent teams from Durham College’s - Process Improvement II course will work with your organization to analyze a challenge currently affecting your organization, and develop a solution that improves quality and/or processes for your organization.
The final deliverables will be agreed upon in at the project scope meeting and will vary by project. Generally, your organization will receive a report, live presentation, or project plan.
Project timeline
-
February 16, 2021Experience start
-
February 16, 2021Project Scope Meeting
-
March 2, 2021Progress Check-in Meeting
-
March 23, 2021Experience end
Timeline
-
February 16, 2021Experience start
-
February 16, 2021Project Scope Meeting
Meeting between students and company to confirm: project scope, communication styles, and important dates.
-
March 2, 2021Progress Check-in Meeting
Meeting with the students and instructor to review project progress.
-
March 23, 2021Experience end
Project Examples
Students will work in teams of 4 and spend 10-15 hours per student working with your organization to support the development of improved quality and/or processes that your organization can execute to get results.
You will need to provide the students with a goal, issue, or gap to focus on. Areas of focus include, but are not limited to, manufacturing, quality assurance, supply chain management, and customer service.
What our students could help with:
- Collect data in relation to an existing problem i.e. customer complain, late delivery, defective parts, etc. By using techniques like brainstorming, focus group, survey, etc.
- Apply SPC in a particular control chart to both service and manufacturing for both available and attribute data in order to analyze data behavior and process variation.
- Apply Process Capability study manufacturing processes in order to verify that the process is capable and risks are evaluated.
- Apply a statistically valid acceptance sampling and calculate the producer’s and consumer’s risk due to the sampling procedure.
- Create a policy and procedure for the measuring system in manufacturing and conduct Repeatability and Reproducibility gage study to validate the measuring system.
- Apply 7 quality tools i.e. fish and bone, Pareto chart, house of quality, flow chart to collect, organize and analyze data.
- Apply some management tools
- Assess/analyze risks by constructing a FMEA (Failure Mode and Effect Analysis) to any service or manufacturing product/process.
- Assess the effectiveness of the current layout and design/suggest a new layout for any manufacturing or office/clinic facility.
- Review and modify or create a new purchasing policy/procedure base on the company’s needs and requirements.
Some project examples include:
- How do we reduce waste and variation and improve productivity in storerooms, office supply rooms, or production lines? (i.e. through a 5S program)
- Turn-around-time has increased and does not meet customer requirements. How can we improve turn-around time by 10%?
- The intake process for Clients/Customers has a high incomplete/error rate. How do we reduce the number of errors on the intake form?
- How can we better understand value from the customer's perspective? Students can perform Voice of the Customer/Critical to Quality analysis to determine what matters most to your customers.
Companies must answer the following questions to submit a match request to this experience:
Will need to provide access to resources/data to complete the project.
Provide a dedicated contact who is available to answer periodic emails or phone calls over the duration of the project to address students' questions.
Be available to attend final presentation either in-person or via videoconference.
Be available for a quick phone call with the instructor to initiate your relationship and confirm your scope is an appropriate fit for the course.
Timeline
-
February 16, 2021Experience start
-
February 16, 2021Project Scope Meeting
-
March 2, 2021Progress Check-in Meeting
-
March 23, 2021Experience end
Timeline
-
February 16, 2021Experience start
-
February 16, 2021Project Scope Meeting
Meeting between students and company to confirm: project scope, communication styles, and important dates.
-
March 2, 2021Progress Check-in Meeting
Meeting with the students and instructor to review project progress.
-
March 23, 2021Experience end