Iterative 3D Printing Process Optimization for Morphace Healthcare Wearable Tech
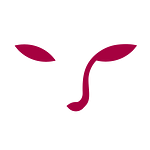
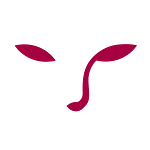
Project scope
Categories
Mechanical engineering Hardware product designSkills
manufacturing processes manufacturing process managementThe primary objective of this project is to iterate and optimize the 3D printing process of Morphace’s electronic mask device to enhance both its usability and manufacturing scalability. Specifically, the project aims to:
- Optimize 3D Printing Parameters: Identify and fine-tune printing parameters for flexible materials, using either 60A TPU, or propose other additive manufacturing alternatives like SLS, to ensure design reliability and material performance.
- Streamline Production for Scale: Refine the design and adjust printing settings to enable the efficient production and assembly of a batch of approximately 100 devices, ensuring that the manufacturing process is both cost-effective and scalable.
Task 1: Optimize processing parameters (estimated ~15 hours)
- Conduct a series of tests to determine the optimal 3D printing parameters for 60A TPU and evaluate potential additive manufacturing alternatives.
- Assess material behaviour under different conditions to ensure reliable performance that can be repeated throughout prints.
- Outcome: A tabulated report outlining the relationship between printing parameters and performance metrics.
Task 2: Iterate design for usability and scalability (estimated ~13 hours)
- Analyze the current CAD model to identify components that can be re-engineered for easier production and assembly.
- Produce a pilot batch using the optimized printing parameters and revised design.
- Conduct usability tests of being skin conformal, then integrate the results into a 2nd iteration of the design with improved fit and device functionality.
- Outcome: Revised CAD design files that integrate enhanced features for both manufacturing scalability and end-user comfort.
Task 3: Process mapping (estimated ~2 hours)
- Document the processes of testing to compile experimental procedures, design iterations, and testing results
- Compile a high-level analysis of cost-benefit tradeoffs during the production process, from getting raw materials to delivering the product, comparing against current state-of-the-art processes employed by competitors (personal care electronics, aesthetic medical devices).
- Outcome: A public presentation articulating the optimization process, validated improvements, and actionable insights for production scaling that the students can showcase in their resumes as a case study in the sectors of health & wellness and personalized wearable technology.
Providing specialized, in-depth knowledge and general industry insights for a comprehensive understanding.
Sharing knowledge in specific technical skills, techniques, methodologies required for the project.
Providing access to necessary tools, software, and resources required for project completion.
Scheduled check-ins to discuss progress, address challenges, and provide feedback.
Supported causes
The global challenges this project addresses, aligning with the United Nations Sustainable Development Goals (SDGs). Learn more about all 17 SDGs here.
About the company
Morphace brings the dermatologist's office home through automated skin treatments and skin health tracking. Like Invisalign reinventing dental braces, Morphace offers a unique convenience through the hyper-personalization of our wearable hardware and data-driven skin health insights.
Portals

